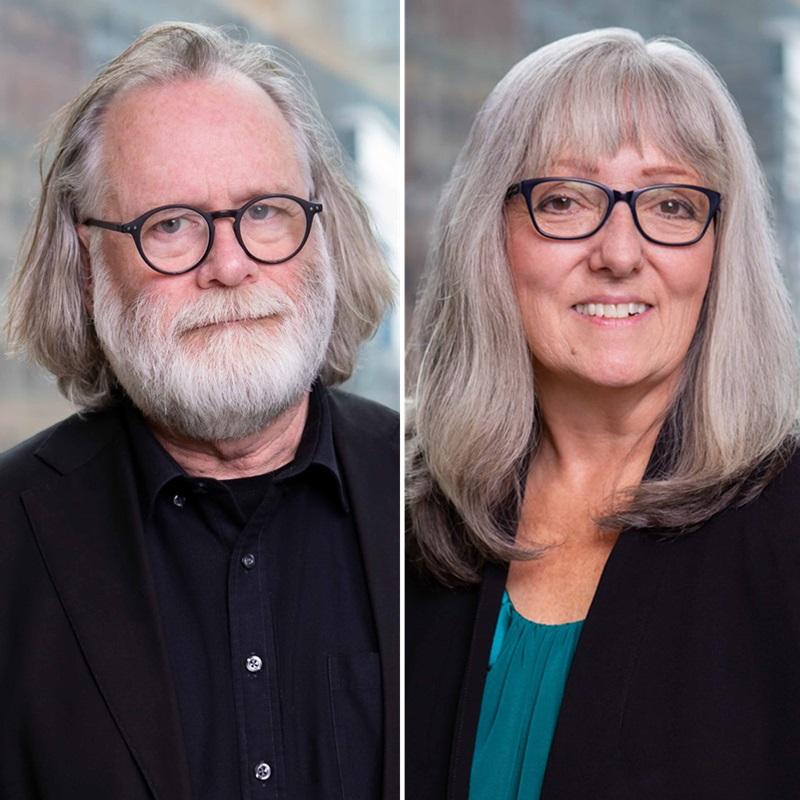
Canadian mass timber construction company Assembly Corp. is looking to fast-track its operations by purchasing an entire factory of robotic manufacturing equipment from a Swedish company.
The firm is partnering with Lindbäcks Group — which also produces factory-built housing and components — in importing the machinery from a 200,000-square-foot facility in Sweden.
“We do panel lines and we’re looking to pre-fabricate our panels inside the factory to be able to ship to the site. This factory does volumetric in Sweden, so they have the entire line and it could be retrofitted to do what we needed it to do because we need floors and we need walls,” Kathy Hogeveen, chief operating officer with Assembly, told RENX Homes.
“The line already is doing it and it’s already proven, and the capacity of the line is very much in line with what we want to get to.”
Currently, the equipment is housed in 31 shipping containers in Sweden. They will be sent to Canada for a planned Toronto-area factory opening in early 2026.
The Lindbäcks deal came about quickly, aligning with Assembly CEO Geoff Cope’s mantra of “not being afraid of change,” company founder and developer Leith Moore said.
What Assembly Corp. has acquired
Included in the shipment are:
- robotic gluing, nailing and cladding equipment;
- stud storage and feeding systems for walls, floors and ceilings; and
- drywall and mudding components.
The annual output for the equipment is expected to be 1,600 housing units.
This partnership arose after a meeting with the Swedish board of trade in June 2024, in which Assembly team members met with representatives who “were obviously very plugged into what’s happening in housing there,” Hogeveen said.
“It turns out he was originally with Lindbäcks and had spent time there, built this factory, the equipment that we bought, so he was very much involved in their entire setup and process," she continued. "Once he got to know our process and found out Lindbäcks was utilizing him to be able to sell the equipment, he approached us and said, ‘Here’s an opportunity that would match exactly what you’re trying to do.’”
Lindbäcks has moved into a new 460,000-square-foot facility, which made its smaller factory redundant.
While the current arrangement calls for both firms to work together setting up the facility in Canada, it’s hoped this partnership will deepen, according to Moore.
Lindbäcks to assist with set-up in Canada
“I think one of the intriguing parts of the partnership is Lindbäcks’ interest in expanding their technology and business experience to Canada," he said. "They’ve been through the lack of labour or housing demand curve that we’re hitting today.
"They probably hit that 10 or 15 years ago and so they’re coming out the other end of that with a lot of experience, and I think they see an opportunity where we have an under-industrialized housing sector in terms of its ability to meet demand."
Before the factory is handed over to Assembly, the Swedish firm will act as a consultant to ensure everything is working as it should.
“Not only are we getting proven advanced technology that will put us at the top end of fabrication capacity or capability, it comes with experienced operators," Moore said. "They’ll be here for year and a half, working with us on setting it up and making sure all the parts fit together and work, but also in terms of an investment interest to help us scale what we’ve been doing for the last few years, which is building and learning.
"And now we can apply their experience and leverage it into thousands of units per year.”
For Assembly, the biggest challenge in getting the new factory operational is simple. “For us, it’s just building the new building,” Moore said.
While the location cannot yet be revealed, it will operate close to active Toronto-area building sites. It will also be portable.
“We can basically put it into an area where there’d be a large market of wood buildings close by and then, as those large new areas get built out, you disassemble the plant and we can rebuild it somewhere else,” he explained.
“Having the ability to get your logistics close to the sites, this brings us a different capacity to how people see costs . . . It’s like the old wayside pits and quarries when you build a highway. It’s kind of the same concept only a lot more sustainable: you do your wood and do your fabrication beside where all the buildings are built and then move on to the next site."
Assembly targets midrise multifamily market
The Lindbäcks robotics will enable Assembly to focus on its key target market - midrise buildings which comprise the “missing middle” of Canadian housing. While pre-fabricated houses are not new, building larger wood multifamily structures has involved getting builders and consumers onside.
“We’ve been at this for six years, and it’s been a constant education of consumers," Moore explained, noting Assembly handles all aspects of the job from approvals to move-in. "Our market is primarily builders, so people who have land and want to create rental assets, or a nonprofit organization that needs a turnkey. . .
"When you are an all-wood building company, what does that mean? Is it solid? Does it last as long? And the answer is yes, it’s all equally solid and it lasts as long or longer.”
Moore also had a message for potential investors.
“We’re dealing with an increasing number of clients who wish to do repeatable, multiple projects per year using an off-site fabrication approach to create rental housing and that’s why I think that rental housing is a good solution for next few years and generates long-term value," he said.
The threat of tariffs on building materials
However, with U.S. President Donald Trump threatening Canada with tariffs, builders are also contending with uncertainty in the housing market.
“Frankly, we’re looking at our supply chain. We have probably 60 per cent, maybe a little more, of Canadian supply," he said. "There’s always pieces inside of pieces but our main elements are local. We are looking at that supply chain to see how we buffer ourselves from what we think is coming."
The potential for tariffs on Canadian wood and timber could actually lead to lower prices for some supplies here in Canada: "It’s an unknown as to whether it becomes good news or bad."