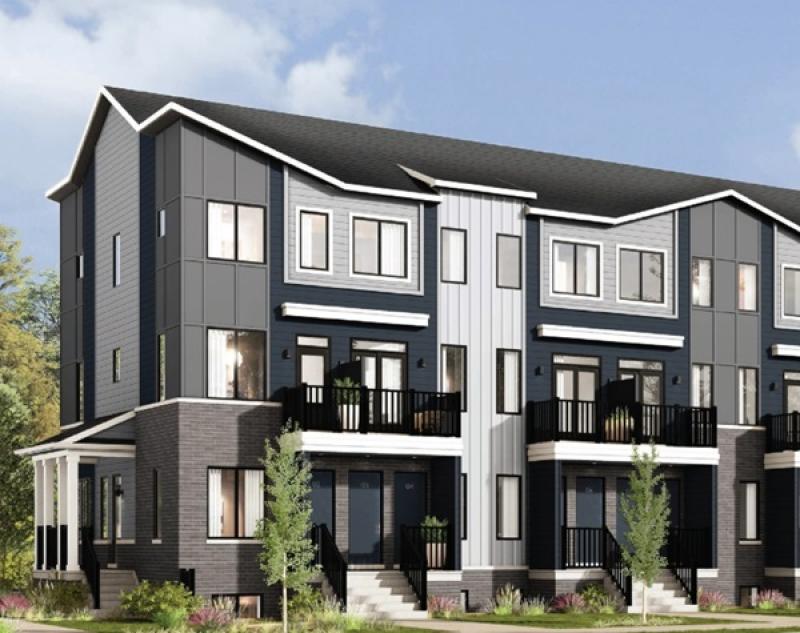
Factory producing major components for its Summit Series of homes has allowed Ottawa-based Caivan Homes to dramatically lower construction costs, shorten timelines and offer new homes for sale starting at just under $350,000.
The Summit Series residences will initially be offered in several developments, comprising townhouses and detached homes, around the nation’s capital.
The inaugural release is in the east-end community known as Orleans Village, where sales opened in November with units starting at $349,990. The village is sited along Lamarche Avenue, in the Innes Road-Page Road area with nearby access to both shopping and entertainment, as well as major roadways and transit.
By the first week of December, Caivan had sold 170 units.
“We know in Ottawa there really isn’t much for new homebuyers below the $400,000 mark,” Jonathan Wiseman, Caivan’s executive vice-president of sales and marketing, told RENX Homes.
“It’s not just how this product was designed from the ground up; after having these conversations with customers and hearing what they needed, it’s about being able to deliver that quickly.”
The firm is now promoting a second Summit Series release in the southwest Ottawa community of Barrhaven, scheduled for later this year. The company expects those homes to begin listing under $400,000.
Caivan's ABIC manufacturing facility
Caivan established the Advanced Building Innovation Company (ABIC) in March 2021 as its 140,000-square-foot factory and office complex where roofs, ceilings, walls, doors and windows are manufactured. The developer says on-site assembly of these components takes as little as 1.5 hours.
ABIC employs in-house proprietary software developed over 12 years, as well as artificial intelligence (AI), robotics and generative design to expedite homebuilding and augment quality, resulting in five to seven homes being produced on a daily basis, or more than 1,000 per annum.
ABIC wasn’t merely designed for efficiency; it’s also sustainable and minimizes land-use waste, materials, and — with only 40 employees — workforce.
Mattamy Homes had a similar idea with its 2007 launch of the Stelumar warehouse in Milton, just west of Toronto. At the time, the 78,000 square-foot facility employed 120 workers to assemble houses in around 10 days before transporting them to nearby subdivisions.
But the builder determined it was not financially viable at the time, and threw in the towel two years later.
Changing times in the housing industry
Much has changed since then, namely advances in technology like AI and robotics that enable ABIC to operate a factory larger than Stelumar, but with only a third of the workforce. The modular, or prefabricated housing market has also begun to take off again as a housing crisis, affordability and a looming skilled trades shortage combine to put pressure on the traditional housing construction industry.
Prefab and modular factories are currently churning out the components for single-family, low- and midrise housing. While these factories represent substantial capital expenditures, fateful building economics leave developers few choices.
Scott McLellan, chief operating officer of Plaza Corp., which mainly builds highrises but also develops lowrise projects in the Greater Toronto Area, said automating at least parts of the homebuilding process can reduce expenses - whether due to cost overruns from dealing with bureaucracies or pay for more expensive trades workers.
“Are you going to be saving money on unions? Probably,” he said.
But perhaps the most significant savings will come from not having to halt construction during winter’s most frigid months — while still paying carrying costs and financing the development site.
“There are times where it should take a month to complete a certain task in the construction world, but it takes three months because of weather,” McLellan continued. “This would certainly cut down the timing.”
Saving time and lowering costs
Construction loans can be difficult to repay punctually, given the myriad of variables involved with building housing. Then comes the cost of paying tradespeople to do large volumes of work at the development site.
“This sort of negates all that," McLellan said. “If you can have a house built in a factory, ship it and install it, it’d be a great time saver, which is going to be a money saver.”
The savings on workforce can be quite enticing, according to Richard Lyall, the president of the Residential Construction Council of Ontario. He cautioned, however, that factory-built homes are only feasible at scale and with the market still in the doldrums, that volume doesn’t exist for many builders.
“The challenge with this is you need some business, some volume,” Lyall said. “You need at least 1,000 units a year to produce.”
Moreover, with fewer projects in the pipeline, Lyall contends construction trades are offering their services at lower, more competitive prices.
“So the rationale, or justification, for moving to off-site construction as an answer to the lack of labour is gone,” he continued. “That doesn’t apply anymore.”
Summit Series
At Caivan, however, the volume does exist, and the homes are selling at a brisk pace.
With floor plans ranging between 900 to just below 1,100 square feet, Wiseman said the Summit Series will be popular with homebuyers for a very specific reason: it’s the type of housing they asked for.
The developer sold over 300 homes at its various projects throughout Ontario during the fall, and had thousands of new registrants and prospective buyers in its sales offices. So, it asked them for feedback.
“It’s not just how these are built, it’s about how this product was designed from the ground up after having all these conversations with customers and hearing they needed a minimum of two bedrooms and a dedicated parking spot included in the price of a home, as well as lots of natural light,” Wiseman said.
The Orleans Village release offers two-storey stacked townhouses, and ensuring units received enough natural light required outside-of-the-box thinking when designing floor plans.
“We’re constantly enhancing all of our design and build processes,” Wiseman said. “It’s all about built-in quality while also driving down the length of the build.”