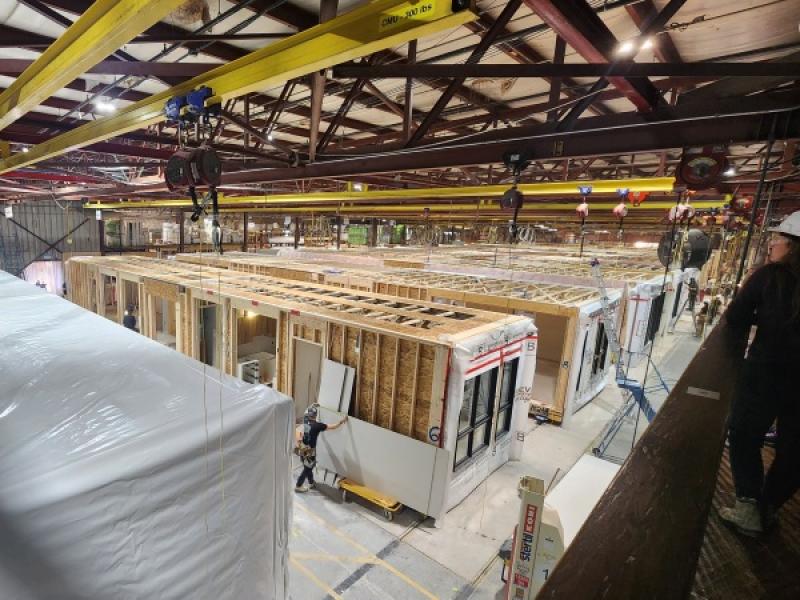
Quebec student housing non-profit UTILE is advocating a framework to lower the costs of modular construction, the biggest barrier to a method it argues can help alleviate Canada’s housing shortage and affordability concerns.
Modular construction — constructing segments of a building in a factory setting, then assembling them at the construction site — has been increasingly promoted by governments and the private sector as a faster way of building housing. A report by the CSA Group said modular construction moves 25 to 50 per cent faster than conventional methods, and some contractors have also reported cost savings.
UTILE COO Gabriel Fournier Filion says modular techniques do reduce construction times, but after building the company's first prefabricated project, a 155-unit midrise complex in Rimouski, Que., he questions whether there are financial savings.
“Prefab is a lot faster . . . but it’s not cheaper and sometimes it’s a little bit costlier,” he said. Compared to a typical project, modular construction costs up to 10 per cent more, he said.
If that cost is not overcome, modular construction will not find widespread adoption, Fournier Filion said. Why, he asked, would a developer invest in prefabrication if the economics do not make sense?
To break down this barrier, the Montreal-based developer has created what it calls a consortium model that emphasizes partnerships with industry peers to establish more market certainty, and hone efficiency with every completed project.
The model is to be applied in UTILE’s upcoming prefabricated projects as part of a study funded by the Canadian government to uncover solutions for the country’s housing shortage.
Minimal modular building in Canada
UTILE, which has built or has under construction over 2,000 housing units across 13 projects, is a newcomer to the modular field. The Rimouski project, which started in 2024, is a pilot to see how the developer can make prefabrication work effectively, Fournier Filion said.
Only about one per cent of Canadians live in modular or prefabricated housing according to IBISWorld. Fournier Filion suggests the conservatism of the Canadian construction industry and its limited familiarity with modular construction are the main impediments.
Though its experience has shown it is not currently a cure-all for the construction industry, UTILE remains deeply interested in modular construction because of its potential.
“If it’s cheaper and faster (than traditional construction), the market will adopt it. It’s a no brainer,” Fournier Filion said.
Today, most prefabricated building manufacturers focus on single-family housing that carries higher margins but lower volume. UTILE is hoping to shift the focus to a low-margin, high-volume model which will need more customers who want to repeat orders and guarantee a pipeline of development deals.
“You need to be sure that you will have the huge volume of orders that will justify this change in order that at the end of the year, you make more profit in absolute terms.”
Another shift to incentivize modular construction is standardizing the industry to help subcontractors understand the scope of their work and be clear about their duties.
UTILE's consortium model for modular construction
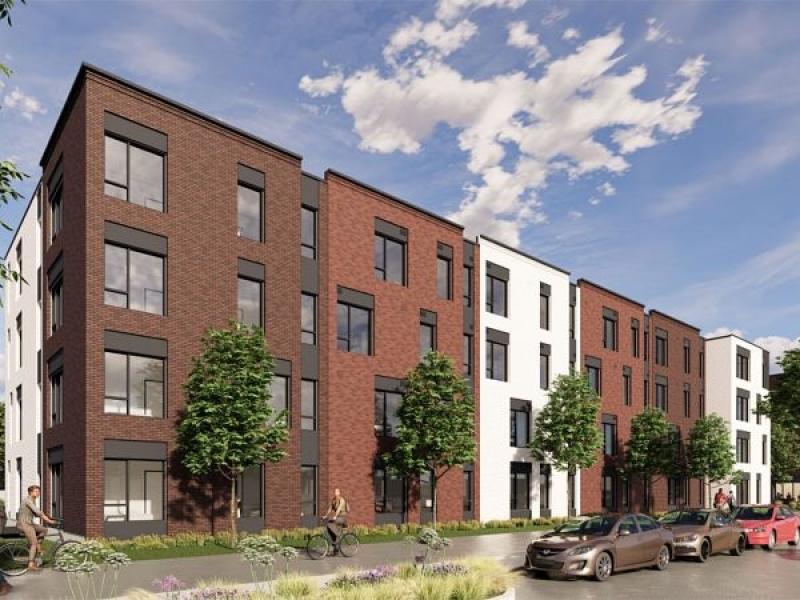
Its proposed solution is a consortium of stakeholders “dedicated to identifying and solving barriers across the modular construction delivery chain,” with a focus on student housing. UTILE has received $4 million from the Canadian government’s Housing Supply Challenge, as one of nine finalists, for development and testing in Rimouski.
The first step is solidifying a long-term commitment. A developer should be dedicated to a large number of prefabricated units so manufacturers can adjust their business model, Fournier Filion said.
Next would be the creation of a permanent consortium between prefab manufacturers, developers and general contractors who will build as many projects as they can in a certain timeframe at a fixed price. This could be achieved with a multi-project contract that will be in effect even if the parties are still working out details for their future projects, a framework UTILE is developing with a manufacturer.
Third is standardization: ensuring there is a consistent, mass-produced module compatible with every project. Standardization makes it easier to improve productivity and for the manufacturer to build rapidly, Fournier Filion explained.
Finally, once a modular project is finished, the costs would be analyzed and the project re-examined to uncover ways the next project could be further optimized.
UTILE is aiming to decrease the costs of modular construction by 10 to 15 per cent compared to conventional means, Fournier Filion said. The framework being developed by this consortium can then be employed by any developer or general contractor.
UTILE's upcoming modular projects
UTILE’s Rimouski project is expected to be finished by the summer — the firm bought the land in May 2024, and plans to have it delivered in July 2025.
The company is looking to apply the consortium model in three more projects: Phase 2 of Rimouski which will add 80 units; an approximately 200-unit project in Trois-Rivières; and an 180-unit development in southern Quebec.
Its overall plan is to build four new projects every year, with one of them being modular.