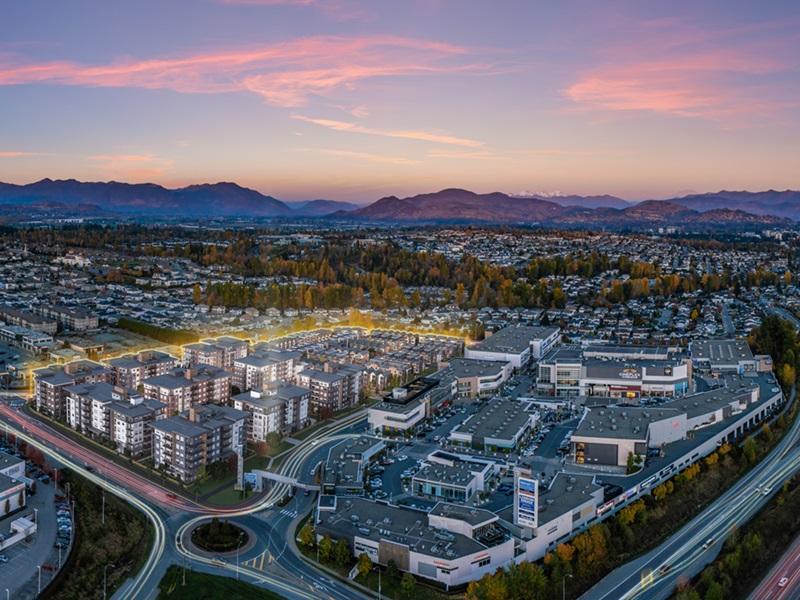
The developer of a large residential community in Abbotsford, B.C. says nearly 80 per cent of the construction materials and installations for the project are being sourced locally or in Canada, a figure most others in the industry should be able to match.
A series of tariffs instituted by the U.S. have gone into effect, with additional tariffs being threatened. Canadian developers are bracing for the impacts of Canadian government counter-tariffs on U.S.-made products.
This will lead to higher material costs, supply chain disruptions, and greater economic uncertainty for the Canadian building industry.
Alf Wall, co-founder of AB Wall, said the company's Highstreet Village project shows a local-first approach can provide a strategic advantage and set the firm up for future success regardless of a trade war. J. Floris Construction is building the project.
Wall told RENX of the 80 per cent of his materials and inputs being source domestically: roughly 16 per cent (of total costs) is concrete, sourced in the Fraser Valley; 12 per cent is lumber, sourced from B.C. forests and mills; and 11 per cent is civil and excavation work performed by local companies. Additionally, Wall says siding/roofing materials, doors and windows are among other items which are mainly sourced domestically.
Wall said carpet tends to be an item that most builders still have to source from the U.S. as most of their supplies are manufactured in southern states.
‘We’re hardly exposed’
"We're hardly exposed," Wall said, noting that most materials not sourced locally or domestically come from overseas and not the U.S. "Generally speaking, appliances all come from overseas, (and) plumbing fixtures are usually (from) overseas."
He said AB Wall's labour is 100 per cent local, elaborating that they don't use any temporary foreign workers. "A lot of the workers are from Chilliwack or Abbotsford," he said.
Highstreet Village is a 12-acre residential community in West Abbotsford that includes 131 townhomes and nine mid-rise condo buildings, comprising an additional 577 units, in a multi-phased development.
So far, about 400 buyers have secured homes in the community, Wall said. AB Wall, a family-run business, purchased the site in 2018.
"In terms of sales, we're about half sold out, and that's mostly pre-sales," Wall said, noting about 95 per cent of the buyers are locals.
He said they're now building the fourth of five phases.
Focusing on using Canadian-made materials, domestic trades and local suppliers, the project has mitigated exposure to external market volatility, an approach that becomes more important as the trade war changes the industry’s supply chain.
But sometimes, determining whether a product or material is truly Canadian can be tricky to nail down. Where is ownership based? Where do the raw materials come from? Who is doing the processing or manufacturing work? Who is the distributor or wholesaler?
For instance, Wall said most of the concrete comes from a Lafarge Canada processing plant in the region. While that company is part of Holcim Group, a Swiss-based multi-national organization, the production and labour is local.
Closing on homes can’t wait on supply chain issues
Closing on a condo deal and getting the buyer into their home can't be slowed down by missing materials, Wall said, "so, you get local suppliers".
If something gets broken during delivery or installation, or needs attention, locals respond quickly. "They'll fix it tomorrow," he said.
Wall said many builders had already been prioritizing local supply chains prior to Trump's tariff warfare against Canada. The pandemic and the supply chain headaches that emerged in 2020 played a role in rethinking procurement.
"It certainly did encourage people to (buy) local," he said. In some cases, that meant foregoing cheaper overseas materials, but those additional costs outweighed the more costly situation of delays and supply problems.
AB Wall is a local company so he sees part of its reputational value is in supporting other local businesses. "We're local developers . . . and we're well known in the valley, so we want to maintain that reputation."
BCCA moves to identify Canadian products
Chris Atchison, president of the British Columbia Construction Association (BCCA), told RENX it's a realistic sentiment for any one developer to pursue and achieve a high percentage of made-in-Canada construction materials and products, especially for builders focused on smaller-scale residential projects.
"The industrial, commercial, institutional and multi-unit residential sectors . . . are significantly intertwined with American trade," he said, noting it remains to be seen how tariffs will play out and how Canadian government reactions could impact our construction supply chain and prices.
The BCCA estimates up to 80 per cent of lumber used in Canadian construction is from Canada; about 80 per cent of cement is Canadian; 45 per cent of steel is domestically supplied and about half of insulation is domestic, to name a few key products.
"We're self sufficient in some key construction materials," Atchison said, but noted many specialized or special-grade products and materials across the spectrum of construction needs do come from the U.S., including a wide variety of HVAC equipment.
Atchison said the BCCA has updated its directory to identify Canadian-made or produced products and supplies with a Canadian icon, similar to what Canadians are seeing now in grocery stores.
"We're proud to be able to do our part as we're facing some uncertain times."