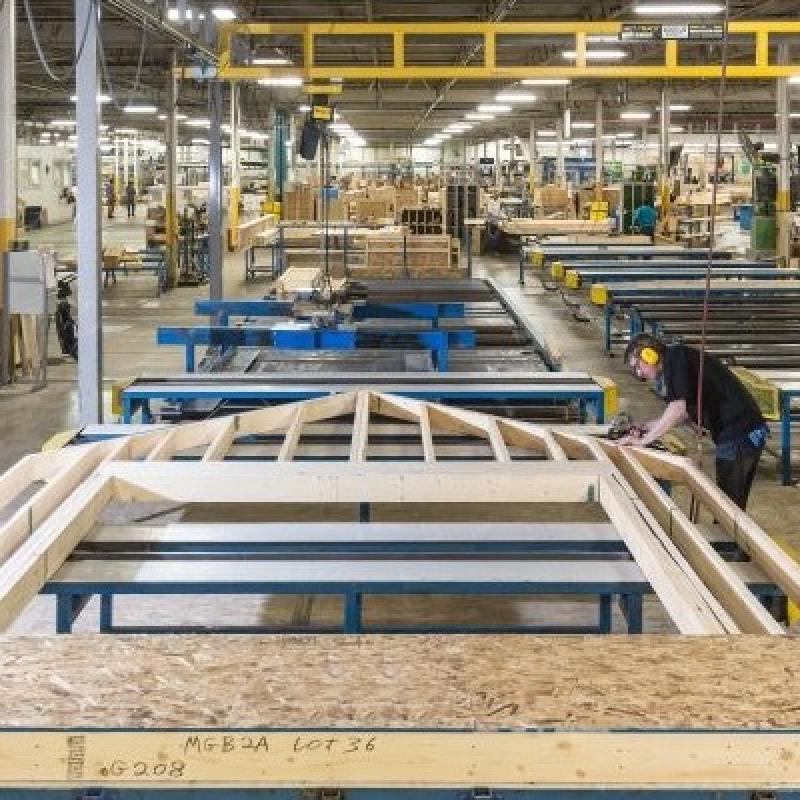
The conundrum over Canada’s housing supply and costs have led to a scramble for solutions. Innovations to build faster and cheaper than conventional homebuilding have been introduced, one of the most notable being prefabrication.
By constructing housing at a factory, proponents argue prefabrication not only builds quicker and more affordably, it creates less waste and boosts productivity.
Great Gulf Group of Companies, a Toronto-based commercial and residential property builder, developer and manager, is a leader among its peers for its early adoption of prefabrication through its H+ME Technology business.
Created in 2007, H+ME Technology produces wall, floor and panel systems for residential builders, and builds prefabricated housing in its Etobicoke factory.
“The objective of the plant is to be a part of a constant improvement of product and technology," Tad Putyra, the president of H+ME Technology and president and COO of Great Gulf’s low-rise division, said in an interview with RENX Homes. "We are not just the manufacturer; we are a platform for an entire concept of the construction.”
Trailblazing in prefabrication
Great Gulf was motivated to create H+ME Technology after its founders challenged the company to be more innovative than its peers.
In the early 2000s, Great Gulf recognized a shortage of skilled labour would be a major challenge for homebuilding in Canada and the U.S. The company also saw the homebuilding industry was lagging on adopting technology.
A McKinsey & Company report published in 2017 comparing various industries found productivity in the construction industry had plateaued or decreased. The problems were the delayed adoption of technology, insufficient attention to design, not enough collaborative planning processes, work stoppages, and disruptions in the flow of materials and labour.
“The construction industry is not exactly the leader in deployment of technology and improvement of productivity,” Putyra said.
This led to questions over how Great Gulf could be protected from potential productivity declines. The remedy was creating H+ME Technology to jump ahead on automated prefabrication.
The benefits of prefabrication
At its 200,000-square-foot Etobicoke facility, wood buildings up to six storeys are manufactured, including stacked condominiums, townhouses and single-family homes. H+ME Technology performs the 3D design, engineering, assembly using robotics and delivery to the site.
Its prefabrication is layered with manufacturing industrial principles, according to Putyra, which adds more value to its products.
“Shorter construction timelines, safer and healthier working conditions. The extra bonus: being able to control production at a much higher level than on a job site would be contributing to sustainability,” he said.
For a 2,000-square-foot-plus house, prefabrication cuts the amount of work hours by at least a third, and eliminates the risk that unpredictable or extreme weather can have on construction.
The 3D design and industrial process allows for more precise material procurement, efficiency gains and uncovering errors, which Putyra said enables H+ME Technology to cut construction waste by as much as 50 per cent, depending on the product.
In a six-storey, 90,000-square-foot apartment made out of engineered wood rather than concrete, carbon dioxide emissions are cut by as much as 2,800 tonnes – equal to taking 600 cars off the road for one year.
Putyra regrets not being exposed to industrial manufacturing earlier in his career. The Etobicoke facility is run by automotive engineers who continuously improve the process and product, which he described as “outstanding.” Lessons can be learned daily and capital can be deployed prudently.
H+ME Technology has built over 15,000 residential units to date, servicing clients such as Brookfield Residential, Laurier Homes and Lindvest Homes.
Expectations for growth in Canada
The debate over Canada’s housing has bled into a conversation over immigration numbers and the shortage of skilled trades. Putyra said H+ME Technology rectifies this problem. The factory employs over 100 people and over 40 per cent of the new hires are new Canadians.
“With a short period of time these newly arrived colleagues are working on a production line building houses.”
Prefabrication, he expects, will expand in popularity across Canada. The shortage of labour will incentivize more companies to explore the idea. Plus, the country has all the pieces in place to deploy the technology and systems, such as companies to build the equipment.
Canada can also learn by example.
European builders have been using prefabrication for decades, so Canadian prefabricators can learn from the successes and setbacks on the other side of the Atlantic Ocean, Putyra said.
To support prefabrication, Putyra recommended the Canadian government provide incentives such as better education, tax measures and aiding with the approvals and standards processes.
H+ME Technology is prioritizing increasing value for customers by improving the process, speed and building performance. Putyra believes Canada is at a period in time when knowledge of the superiority of prefabrication over traditional buildings will become more widespread.