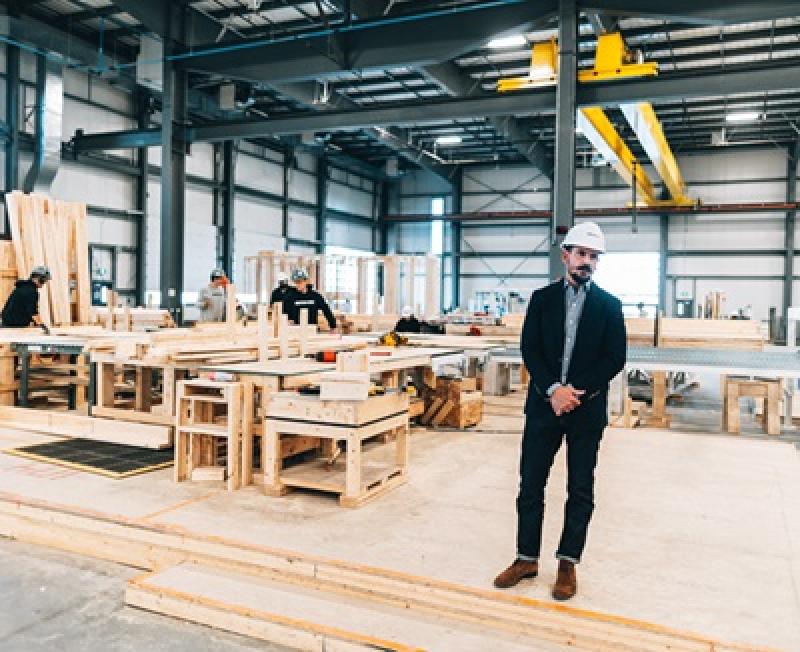
Frank Cairo speaks about Canada’s housing shortage with the passion of a man on a mission. That’s because he is on a mission . . . to promote AI, technology and factory-based mass production to vastly increase housing supply.
As a founder and co-CEO of Ottawa-based Caivan Homes, Cairo and partner Troy van Haastrecht have invested tens of millions into one of Canada’s most highly tech- and artificial intelligence-enabled manufactured homes facilities to complement their homebuilding business.
Caivan’s 140,000-square-foot Advanced Building Innovation Company (ABIC) facility in southwest Ottawa was completed three years ago and produces between four and six homes daily, about 1,100 per year. It makes Caivan the country’s largest producer of manufactured housing – with just one shift of 40 or so workers toiling five days per week.
“We are talking about the need for millions of homes and we are producing, currently, thousands,” Cairo told RENX Homes, acknowledging the scope of the challenge facing a country experiencing record population growth. “We are talking about a quantum that is so hard to even conceptualize that it really is an all-hands-on-deck moment for all of us.”
By “all of us,” he means the homebuilding and construction industry as well as governments at all levels.
Plans to expand ABIC facility
Cairo has plans to increase production by adding additional shifts, new automation and expanding the facility to 240,000 square feet. That would allow Caivan to manufacture up to 5,000 homes per year.
For now, however, Caivan produces all of the homes for its Ottawa-area building sites at ABIC. It has, on occasion, also manufactured homes for other builders – something the company will likely do more as it grows its production capacity.
“This capital investment you see here today is about $70 million in a ship-to-shore outfit, which really hammers home the fact that scale is critical,” Cairo said. “Amortizing a capital expense like that over a low volume will not be feasible.”
Caivan was formed in 2009 by Cairo and van Haastrecht and has become a force in the industry. It is developing a variety of housing types at several sites in both Eastern Ontario and the Greater Toronto Area.
Already Ontario’s third-largest homebuilder and active in 50 communities, its development pipeline includes land to build up to 30,000 homes in each of the two markets. That demonstrates the kind of scale Caivan can provide if the right conditions for these projects are put into place.
The benefits of manufactured housing are well-known within the industry.
Land entitlements critical to achieve scale
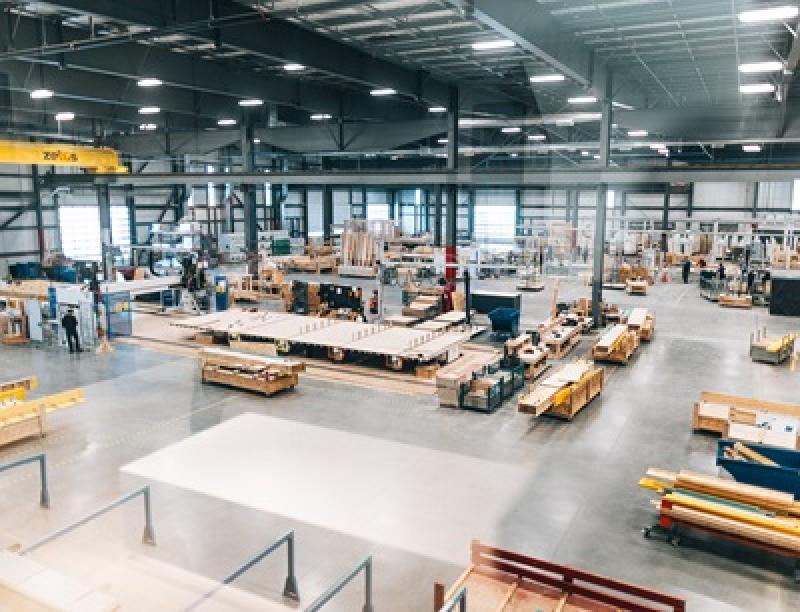
In spite of this, Cairo believes the homebuilding sector has actually stepped back from its history.
During a facility tour, he shows a visitor a black-and-white promo video of a manufacturing plant in Indiana which built 50,000 homes per year - in the 1950s and ‘60s. “We’ve lost our way,” he states.
Today, to meet the country’s projected need for at least 3.5 million new homes by 2030, Cairo provides a list of conditions that must be met, including: more skilled trades, more manufacturing facilities such as ABIC and more buy-in from all levels of government to entitle land.
For Caivan to scale up ABIC, and have other companies do likewise, requires a steady stream of land on which to place those homes.
“The short story is in order to build productivity in our sector we need land that is entitled to take the product we’re producing. I can’t turn my factory on and off based on the flow of a land development or a site-plan approval,” Cairo said.
That means quickly entitling land that is already slated for development and within existing urban boundaries.
“We have to have lockstep co-operation with all levels of government to make sure that as we scale up our factory, for example, there is a scale-up of land development approvals as well.”
Many benefits to manufactured housing
Homes can be mass-produced just like automobiles, he stated, but unlike those vehicles, housing units can’t be stored in a parking lot until there is demand.
They go out the door to the development site, where the components are placed on foundations and assembled. The shell of a dwelling can be complete in as little as 90 minutes, whether it’s a stand-alone home or a unit in a multifamily building.
And the quality is much higher compared to on-site construction, Cairo said.
“A reduced ecological footprint and improved sustainability is a big factor,” he said, beginning to list the benefits. “The quality we can achieve here is surgical. The safety and quality of the work environment is a big factor for workers.
“Finally, scalability and affordability of the product to the consumer is a big driver.”
To these ends, Caivan and ABIC are among the builders pushing the industry back to the future, in a sense. The company has a significant artificial intelligence and tech component to its workforce – literally designing and building the dozens of platforms and tools it needs to automate manufacturing.
"The part that's broken needs to be fixed"
“The desire was never to manufacture or become a software company or to innovate for the sake of innovation,” Cairo explained. “We really have taken an approach where the part that’s broken needs to be fixed and getting scale with the home structure, and quality with the home structure, and better predictability was a big priority of ours.
“That just led to, serendipitously, advanced manufacturing as the way to get there.”
That philosophy led the company into areas it had never dreamed of going.
“Most of what I’ve showed you . . . today doesn’t exist in the world,” he said, following a tour of the facility. “We didn’t set out to become a software engineering company, (but) we have a mechatronics department, a software engineering department, we have experts in mathematical optimization and so on because we had to develop some of the tools and techniques that we are now using.
“These have all been built in-house by our team.”
From design to materials ordering, billing to transportation, AI and technology are involved in all aspects of the process.
More sustainable housing
The impact on sustainability is also significant. ABIC is a fully electric facility, benefiting from Ottawa’s clean electrical grid. The homes are well-constructed, meaning they save on energy even before additional sustainability features are added.
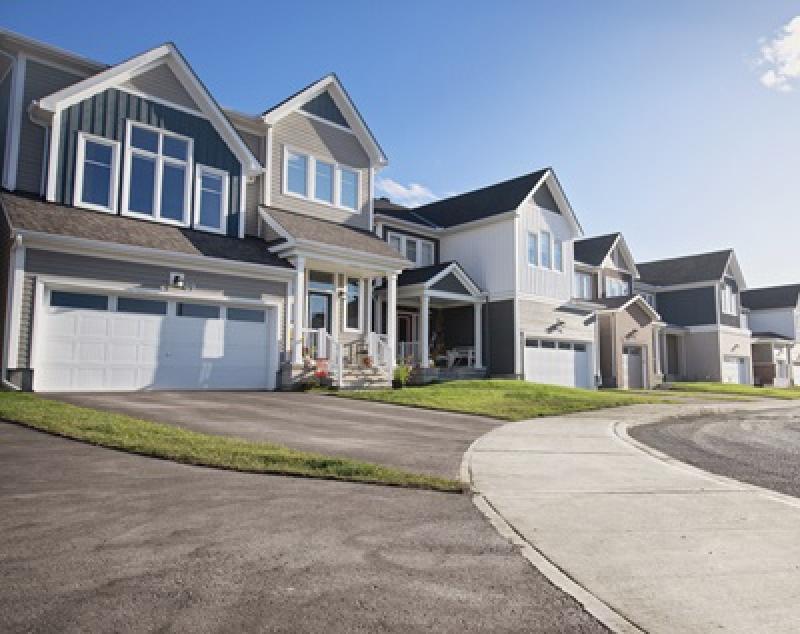
The AI-controlled and fully automated manufacturing process means not a single piece of wood is wasted. Every cut is tracked and leftover pieces are logged in the database for use in a future component.
“Nothing that comes in goes out as waste,” Cairo said.
The system works well for many forms of housing, up to and including mid-rise type developments.
“It’s really anything ground-oriented. If it’s a wood-frame feasible form, manufacturing is a great solution,” Cairo explained. “A one-off custom home in an urban area with very tight access constraints may not be the best candidate.
"But with scale and decent enough volume of housing, anything ground-oriented can really be built well with a manufacturing technique.”
Standardization, yes. Cook-cutter design? No
While some standardization is required to allow for scale and speed of production, manufactured housing doesn’t mean producing cookie-cutter designs. The platform can accommodate a wide range of individual elements at the design phase - which Caivan also handles in-house.
“Because the designs are so autonomous, we don’t need standardization to manufacture well. The standardization is important, though, to get cost reductions and get the scale up,” Cairo said. “Right now, down our line every day is a unique, individual home that is customized to the individual preferences of the customer.
“Standardization helps obviously with cost and speed but our systems are constantly autonomously adapting to whatever it is we are producing. So yes, we have a standard list of starting points for homeowners to pick from, but the level of customization is surprising when you look at all the upgrades and options that can go into a home."
Cairo also notes one other vital aspect of Caivan’s growth and ability to innovate. It remains a private company and its owners have the flexibility to follow their own business direction.
“One of the flexibilities we’ve had in doing it our own way is we have not had to raise capital from mezzanine lenders or venture capitalists or equity markets of any kind,” Cairo said, although Caivan does have financing from a group of Tier I lenders. “We’ve really built this on our own, which has given us a tremendous amount of freedom.
“It could’ve maybe happened faster, but we’ve really preferred to keep control of this on our own.”