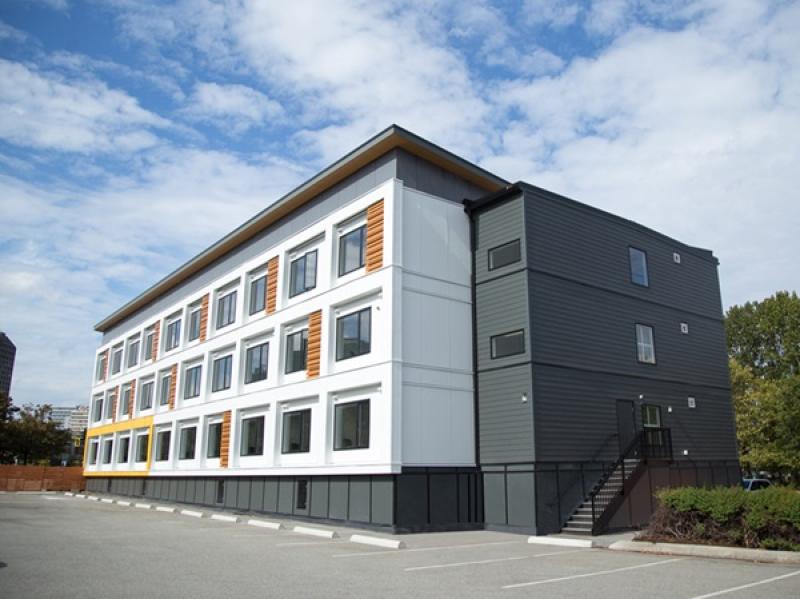
ATCO Structures has acquired Dexterra Group’s NRB Modular Solutions — a $40-million bet it’s confident will pay off in a country beset by exorbitant building expenses, home prices and labour shortages.
“Modular construction has less impact on the local area because there’s a shorter period that’s spent on the project site, there are less materials, there’s less labour actually required on the physical construction site,” Adam Beattie, president of ATCO Structures — a division of Calgary-based ATCO Ltd. — told RENX Homes.
Substantive, he added, for builders who often struggle with the sheer economics.
“The ability to bring automation into the modular construction process is a massive advantage when you have limitations on access to labour.”
One reason construction timelines protract in major metropolitan markets is tradespeople cannot afford to live in them. Canadian winters also hinder production on construction sites, but that doesn’t mean developers get a break on steep carrying costs tied to their financing.
Beattie said modular construction significantly reduces labour outlays and construction timelines. However, he added that modular isn’t “a complete solution to all residential construction,” but that it has a place in the ecosystem and, as it grows, will augment development economics.
“Modular really provides a sweet spot to maintain productivity all months of the year, or move some of that work off-site, where you get a better controlled environment and better management of skilled labour to be productive for longer periods of time,” he said.
Long-term horizon for NRB Modular
ATCO Structures’ decision to acquire NRB Modular Solutions — which is based in Grimsby, Ont., between Hamilton and Niagara Falls — is part of a long-term play by the firm. It also recently acquired Lethbridge-based Triple M Housing, the largest manufacturer of factory-built modular housing in Western Canada, at the beginning of 2023.
NRB bills itself as Canada's largest builder of modular housing solutions in the country.
And NRB is very much a strategic acquisition. It has robust business operations in British Columbia and Alberta, can easily supply remote areas of Saskatchewan, and it has an existing base of clients in Ontario.
The acquisition will also make expansion into Québec a more achievable endeavour.
But a salient part of ATCO Structures’ long-term horizon is the ability to forge partnerships, and NRB is active in the affordable modular housing space, which is touted as a way to alleviate concerns for those in precarious housing situations, and in some cases, even homelessness.
With NRB’s expertise, that may open the door to fruitful pacts with governments like the City of Toronto, which launched the Modular Housing Initiative four years ago as part of its larger HousingTO 2020-2030 Action Plan.
“Many levels of government are looking for solutions to rent affordability, housing affordability and homelessness,” Beattie said. “They’re seeking collaborative solutions to come up with smart, or new, innovative ways to resolve those concerns — which are societal concerns — quickly.
“Skilled labour moves towards multifamily and affordable housing developments, changes in government policy as well, and government promotion of modular has been quite significant.”
He added that Canada’s growing population also presents opportunities for modular construction in the industrial sector, where supply for a time was unable to meet rapacious demand due to recent transformations in the e-commerce chain - and in other segments.
Addressing the student housing shortage
The Canadian government has granted an excess of international student visas, highlighting conspicuous need for student housing, for which, Beattie said, modular design and construction are perfect.
University enrolment in Canada began skyrocketing in the 1990s, however, most higher-learning institutions across Canada haven’t invested much in sufficiently developing new dormitories. That could open the door even wider for development and construction partnerships.
“Modular aligns well with that kind of design and building setup, because there’s a lot of consistency around room configurations, and the finishes and the operation of the building,” he said.
“Dormitory-style for university or post-secondary education facilities are well-aligned with getting value from modular construction, where you can get repetitive designs that are quite consistent — that really suits modular productivity and investment.”
Modular housing is neither new nor established — and that muddles the evidence for how much money developers can save, said Michael Geller, a planning development consultant based in Vancouver.
However, having written a thesis on modular housing as a University of Toronto student in 1970, the now mostly-retired Geller, who has worked as an architect, has spent over five decades championing modular housing.
Geller noted while there’s scarce cost-saving data for multifamily modular developments, in the more entrenched single-family sector, developers regularly shave outlays by 10 to 15 per cent.
“I can say with certainty there are overall construction cost benefits, and they will get better and better as we become more accustomed to using off-site construction,” he said.
Geller anticipates another decade will pass before modular home construction becomes standardized, but he pointed to endorsements from Sean Fraser and Ravi Kahlon — housing ministers for the federal and B.C. governments, respectively — as auspicious signs.
But simple economics, ultimately, will force the hand of innovation, Geller added.
“We simply don’t have enough trades and that’s going to become the imperative to make better use of manufactured housing.”