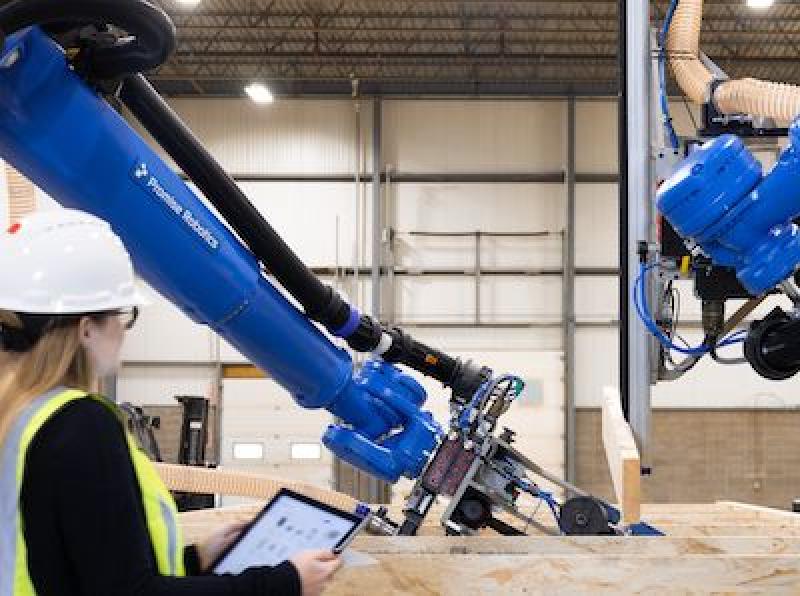
Promise Robotics, a Canadian artificial intelligence (AI) company developing a cloud-based industrial production platform for robotic construction and assembly, plans to use its technology to build homes faster, more sustainably and more economically.
It took a step toward achieving that goal at a wider scale with the Oct. 31 announcement it had raised US $15 million in Series A funding, bringing its total amount raised to date to US$25 million.
Investors were impressed not only by Promise Robotics’ platform, but by the experience and track records of its two founders, their ability to show what the company is capable of now, and the potential its system offers for the construction industry in the future.
Promise Robotics ambitiously estimates that, for every million new homes built using its platform and turn-key production factories, it can help the building industry save $130 billion in costs, reduce greenhouse gas emissions by 560 metric tons and generate 16,000 new categories of jobs.
Promise Robotics’ co-founders
CEO Ramtin Attar was originally a design architect before joining Autodesk — an American multinational corporation that makes software products and services for the architecture, engineering, construction, manufacturing, media, education and entertainment industries — where he was a research and development executive heavily involved with AI and robotics for 13 years.
Attar met Reza Nasseri – an Order of Canada recipient who founded Edmonton-based homebuilding company Landmark Homes in 1977 and robotic residential construction firm Acqbuilt in 2003 – while they were both speaking at a robotics conference in Banff, Alta.
The two entrepreneurs started talking, realized they shared similar goals of enabling the construction industry to harness automation to produce more affordable housing, and launched Promise Robotics in 2020.
“We essentially took all the challenges that we’ve known from our own firsthand experience in applying automation over the last two decades and re-envisioned the future of automation as such that we could bring it at scale,” Attar told RENX. “They're not actually buying robotics from us. What they're getting is two decades of expertise that’s embedded.”
Removing risk for builders
While automation and prefabrication have long held massive potential in enabling the construction industry, builders have largely been reluctant to invest in costly factories and endure years of trial and error to achieve operational success. Promise Robotics, its founders say, removes that risk.
The company uses the same robots employed in auto manufacturing plants. The earlier stages of its development involved building its AI engine, computer vision and robotic tooling to instruct the robots what to do, how to do it and how to collaborate with each other, as opposed to the repetitive tasks they do when assembling a car.
“That allows us to bring a very flexible, intelligent, compact robotic system that essentially reduces what would have otherwise been a very big capital expenditure in setting up factories, because you're now using the same robots to do your framing and to put the drywall on it,” said Attar, who noted the off-the-shelf robots cost about $150,000 each before Promise Robotics adds its technology.
“You can drill all the holes and you can do all of those things. You're essentially training these robots to have incredible skill-sets that previously weren’t available to them.”
Attar said five or six robots, working one eight-hour shift per day, can produce the components for 25 to 40 single-family homes every month. That number could be tripled if they’re operating 24 hours a day.
“The customers and partners don't actually need to worry about the robot maintenance and the robot operations,” Attar said. “All they need to know is they have X number of houses to produce and, based on that, we can go up and down with the robots.
“You're not creating a custom factory. We deploy these in warehouses in common spaces with minimal infrastructure. You’re basically using the same electrical load. That gives us a lot of scalability in terms of how and where we deploy these.”
Reducing skilled labour while increasing speed
The building components are created for rapid precision assembly so skilled tradespeople, which there’s a severe shortage of in Canada, aren’t required.
Promise Robotics will provide instructions to labourers and Attar said a fully enclosed single-family home can be assembled to the lock-up stage — with windows, doors and waterproofing — in six hours.
Promise Robotics started in an Edmonton micro-factory. Next spring it will move to a larger facility in the city where it can expand on the range and volume of products it creates.
The company is looking to expand partnerships with builders so, starting in 2025, it can move into markets across Canada and beyond.
While the initial focus has been on stick-frame construction, which can go up to six storeys in Canada, Attar said Promise Robotics’ technology will enable it to handle assemblies involving metal, cold-formed steel, mass timber and more. It can also be applied to buildings other than homes.
“What we look for are the most common building assemblies and construction techniques in different forms of construction that can stand to be industrialized in order to be applied at a scale,” said Attar. “We're not trying to create custom equipment and custom automation. That doesn't scale.”
Partnerships with builders
The company has developed a joint model with builders that provides them with the option to work with a Promise Robotics factory or own their own facility, which Promise Robotics would operate. That enables partners to focus more attention on building and growing their businesses.
“You just supply a design and we turn those designs into manufacturable components,” Attar said, “and we can actually pass those instructions through the cloud to any robots.”
Promise Robotics goes through an extensive economic analysis with each partner and Attar claims using its system won’t cost any more than what builders are currently spending — but will significantly increase the speed and potential volume of construction.
Though initial manufacturing is happening in Edmonton, Attar and others are based in Toronto and there are also team members in British Columbia and overseas. The company currently employs about 30 people who primarily specialize in robotic engineering, AI, machine learning and computer vision software.
“The ironic thing is that even though we are a robotics company, our gross function is driven by how many homes are built and not by how many robots,” said Attar. “We’re actually in the business of reducing the number of robots as long as we can increase the number of homes that are built.”
Promise Robotics’ investors
The latest funding round was led by Horizons Ventures with participation from Radical Ventures and the Public Sector Pension Investment Board, as well as strategic investors including United Brotherhood of Carpenters, Relay Ventures and Alate Partners.
The new investment will be used to commercialize Promise Robotics’ factory platform production and expand the intellectual property rights associated with its system.
“Bringing the investors in is not just about their money, it's about their shared vision and passion for what we do,” said Attar. “We were very diligent about how we went about fundraising and who we talked to.
“Basically the largest AI-focused venture capitalists in the U.S. and Canada have invested twice, and we have one of Canada's largest pension funds.”