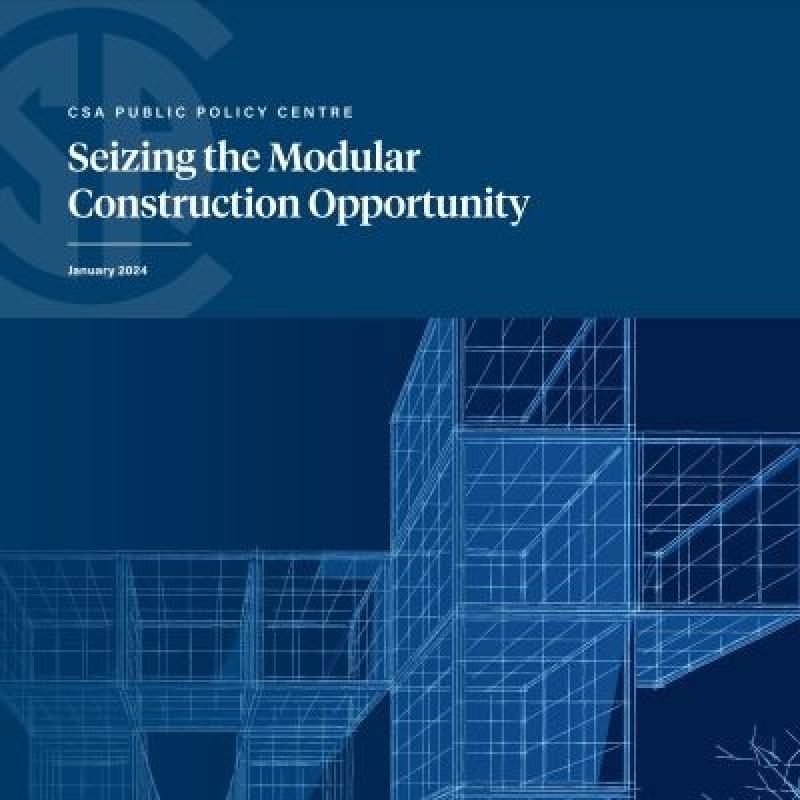
Modular construction is a way to rapidly, affordably and sustainably build the housing, hospitals and long-term care homes Canada needs as its construction industry faces multiple pressures, a report from the CSA Group says.
The Canadian standard-setting non-profit based in Toronto published Seizing the Modular Construction Opportunity through the CSA Public Policy Centre. The CSA Group develops standards for sectors such as construction and buildings.
With the report, CSA Group wanted “to help government and policy makers understand some of the opportunities and challenges around truly seizing the benefits of modular,” Nevena Dragicevic, a manager of public policy at the CSA Public Policy Centre and co-author of the report, said in an interview with RENX Homes.
In the report, Dragicevic and co-author Kinza Riaz point to the supportive role modular construction can have as Canada deals with a housing gap, a shortage of construction workers and an aging population.
She said modular building techniques have the potential to cost effectively and rapidly facilitate construction of the buildings Canada needs, but an enabling environment is needed to reap those benefits.
Addressing Canada’s problems
The report lays out a series of issues Canada faces that could be eased by using modular construction.
It cites research finding hundreds of thousands of workers are expected to retire during the decade 2019 to 2028, productivity is plateauing, and construction costs have jumped 51 per cent. Canada’s population is getting older and getting larger, but there is a deficit of 4.3 million homes and a need for 199,000 long-term care beds by 2035.
Plus, Canada’s construction sector generates four million tonnes of waste per year and only 16 per cent is recycled.
Modular construction can help address these issues, CSA Group argues. Construction finishes 25 per cent to 50 per cent faster than by utilizing conventional approaches. A survey of North American general contractors who used modular components found nearly half reported savings of at least 10 per cent.
For sustainability, standardizing the parts used in modular construction enables reuse and recycling, which reduces the need for raw materials. Buildings can be repurposed and moved to other communities or recycled, Dragicevic said.
Studies cited in the report found modular construction can cut waste by up to 46 per cent and reduce greenhouse gas emissions by as much as 22 per cent. Embodied carbon can also be reduced by another means, as modular construction enables repurposing of buildings or components, rather than demolition.
“We know that Canada faces many challenges around labour productivity, sustainability issues. Modular can help with all of these challenges,” Dragicevic said. Modular construction is not an “all-or-nothing” approach either, she added. It can be combined with on-site construction to gain at least some of the benefits.
The limits and barriers for modular construction
But CSA Group does concede there are restrictions to modular construction.
- It may not be well-suited for certain building types due to the mass production of components.
- The need to transport modular units from a factory to a site increases the logistical costs and risks.
- Modular construction can have heavy front-loaded costs that create potential for liabilities like having modular units accumulate in storage if a project gets delayed.
- Though not unique to modular construction, “the financial stakes can be higher for modular construction because most of the investment is required and spent upfront,” the report states.
Other potential issues include the fact that few people in the construction industry and buildings sector understand modular construction, CSA Group says, and the bodies that issue construction permits and perform inspections also lack experience with modular buildings.
Commonly used public procurement methods for construction projects are said to be “inherently at odds with modular construction methods.” Modular construction does not fit nicely with current financing practices from private and public lenders, which limits the funding for a modular project.
It may not be possible to perform a full inspection of the modules that arrive on site, presenting another challenge. The CSA A277 standard for prefabricated buildings can certify a manufacturer’s products in the factory, but not all provinces and territories require the certification.
Dragicevic said CSA A277 is being formally recognized or referenced in the national and provincial building codes, and Ontario and B.C. issued guidance material on how to approve and inspect modular buildings.
Having a more supportive environment for modular construction
To overcome these gaps, Dragicevic said there must be more supportive building codes in Canada for modular construction. She also recommends more education about the process for regulators. Without better education, projects will get delayed and limit the advantages of modular construction.
Procuring modular builds could be made easier with more collaborative procurement methods, such as engaging manufacturers in design and planning earlier in the process. If a modular builder has proven their value, they could be added to preferred vendor lists.
Easing the application process for low-cost government loans for housing developments could address financial constraints, the report states.
The funding for affordable housing development in the National Housing Strategy could be opened for modular builders, for example. The federal government could also “provide and publicize guidance for private lending institutions to create more financing options for modular construction projects in the open market.”
Finally, forging partnerships between academia and the industry to study the Canadian modular construction landscape would be valuable, CSA Group says.
Dragicevic said there is “a lot of excitement” and increasing attention about modular construction from policymakers, so CSA Group hopes to see a more enabling environment for the sector.