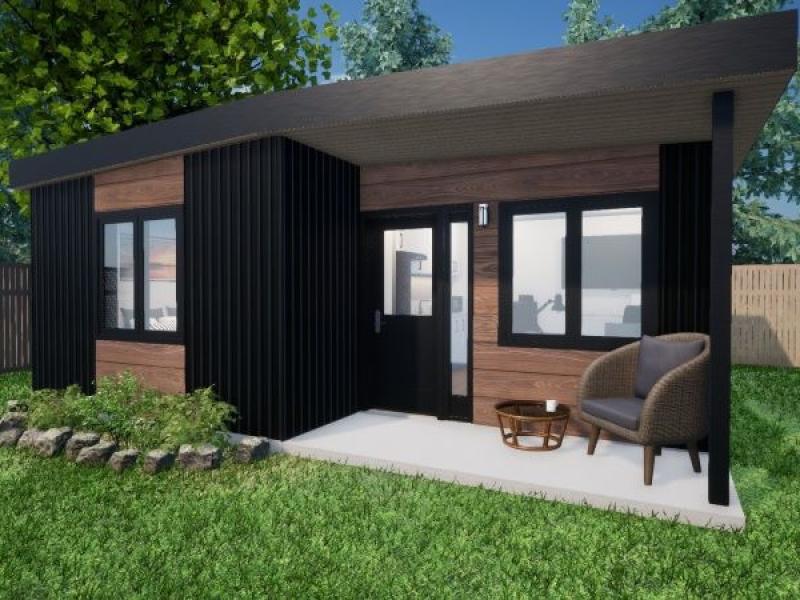
Through its line of modular homes, Pacd Homes believes it has found a way to reduce costs by rapidly building the components for smaller-sized housing in factories.
Guelph, Ont.-based Pacd was founded in 2017 by Blue Valley Building Corporation to take an automotive assembly line approach to manufacturing and designing homes, according to president Jim Marshall, who leads both companies.
After initially shipping materials and assembling wooden panels on-site, the company shifted to fully modular homebuilding for accessory dwelling units (ADUs) and laneway suites at its Guelph facility.
Under its modular construction model, housing components are manufactured at the facility, then shipped to a destination. On site, a small team can assemble them and finish the residence, building a home in a few weeks.
“We’re very focused on small and affordable models. We’re trying to attack that middle belt. Our products have all been built for that purpose, as well as trying to bring down the price of owning a home,” Marshall said in an interview with RENX Homes.
How Pacd works
Pacd currently operates a factory smaller than 10,000 square feet where a team of 10 builds the proprietary components that are then assembled to create its housing products.
David Calder, an R&D manager at Pacd, said the company prefers smaller footprints. Its desired production model is for low-capital-cost factories that can be located “where the homes are to be built” and, just like those homes, can be constructed rapidly.
An interested buyer purchases the desired housing design from Pacd, which can be delivered by a pick-up or flatbed truck, Marshall said. The houses are designed to be easily assembled; two people can pick up a panel and assembly requires interlocking two panels into each other and sealing them with a stud.
Homes can be finished in three to six weeks by a single team, Marshall said, and parts can be transported to remote areas. The process is quicker and less disruptive than conventional homebuilding, he added.
“Our homes, they go in a truck, they ship easily, come off a truck easily. They’re built to be affordably transported and assembled on site,” he said.
Pacd is creating a video so people can learn how to assemble the homes, further indicating the direction it wishes to go in making homebuilding accessible.
The materials Pacd uses offer a 30 to 40 per cent improvement on carbon footprint, and a similar reduction is achieved during assembly, Marshall said. To further cement its green features, the homes are equipped with a heat pump for natural-gas-free heating.
“Our operating, from a carbon footprint, is very low. Because there’s energy-efficient design, it’s airtight, and then just the nature of the fact it’s a smaller construction than typical (homes),” Calder said.
Pacd’s housing models
Pacd offers five models ranging from a one-storey, one-bedroom, 365-square-foot ‘Pocket’ to a two-storey, three-bedroom ‘Leacock’ that is 860 square feet.
The Pocket costs $188,000 and Leacock is priced at $335,000.
The units are designed as a laneway house or an ADU. Greater attention has been put on these housing types as part of the solution for housing affordability and accessibility because they can be placed on the same property as an existing home, where regulations allow it.
Twenty of Pacd’s two-bedroom, 585-square-foot units are being assembled in Guelph as part of a private student housing project.
It also has ADUs in Toronto for retired clients renting out their main homes for additional income.
Dealing with regulations on ADUs
“It’s an exceptional time for modular building,” Calder said, because the technique means houses can be constructed faster – another factor that can help Ontario, or other provinces, meet high new housing targets.
Calder also highlighted the advantage of having most production work done indoors at a time when labour shortages are raising construction costs and challenging the industry.
To draw in young adults into the construction industry, Pacd is working with Toronto Metropolitan University, the University of Guelph and Georgian College to spark interest in a homebuilding career, Calder said.
Marshall said every municipality has its own rules relating to ADU and laneway housing, but said there are initiatives in the works to unify the regulations across Ontario.
“You’re starting to see a move toward a common ADU. If you look at say, Toronto, it was one of the first to go in with the laneway suites, then they brought out the garden suites, and they’re starting to revise. We’re getting a better understanding of those rules and regulations. We anticipate it to be less cumbersome in the future.”
This would be a big benefit to the modular homes industry, as would pre-approved plans to accelerate the permitting process. California and Washington State in the U.S. took up similar reforms, he said, and were successful.
Currently, Pacd is also working on initiatives to create pocket communities, a neighbourhood of smaller-sized housing to help reduce costs, and four-storey modular housing projects with another partner.