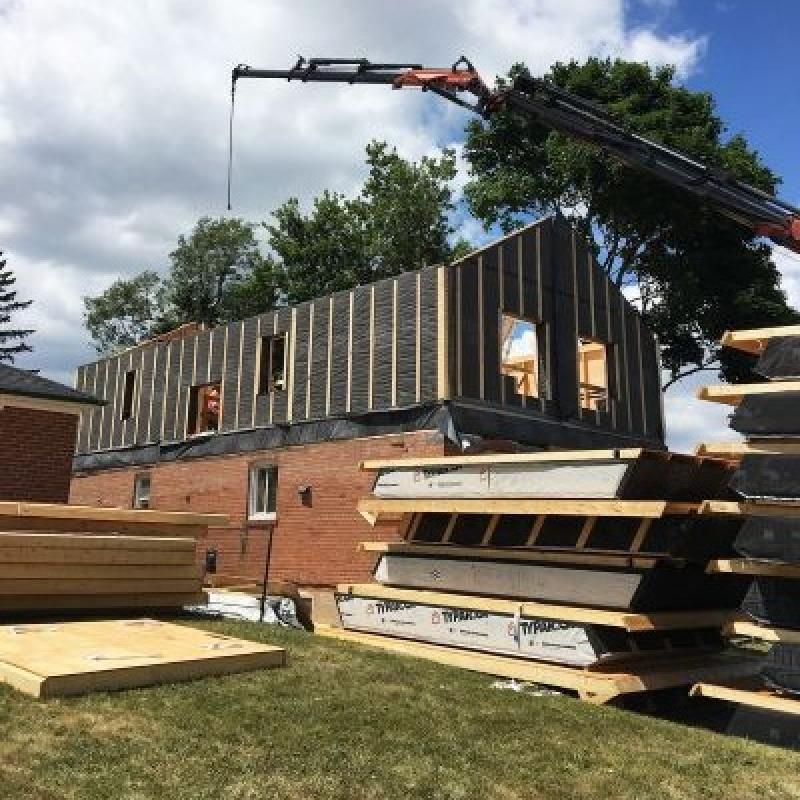
Delivering sustainable homes at speed is the driving mindset for Simple Life Homes, a growing Brighton, Ont.–based prefabricated homebuilder that seeks to serve a range of customers.
Founded by CEO Jeremy Clarke, who started the business in 2012 and devoted fully to the company in 2016, Simple Life manufactures the components for single-family and multiresidential housing from its 8,000-square-foot facility. Then those panels are shipped off to the site where it can be put together in a matter of days.
Its products are built under the Passive House standard that emphasizes energy efficiency through air tightness and insulation, and are built using low-carbon building materials.
“We’re trying to be quicker, we’re trying to be more efficient, trying to be more cost effective, trying to be more sustainable,” Clarke said in an interview with RENX Homes.
These attributes make prefabrication one of the best ways to introduce more housing and bring down costs in Canada, he added.
A former pilot for Air Express Ontario, Clarke has worn many hats in his professional life – sales, financing, carpentry, renovations and home construction. Simple Life is the culmination of the skills he acquired from all those sectors, he said.
A prefab system for 'all shapes and sizes'
Simple Life’s wood-based prefabrication system outputs its products as a fully engineered package that contains the panels made at its warehouse, then loaded onto trucks and shipped to the site. Once there, the panels are assembled one by one with a crane and a few workers. They are designed for simple construction using screws and pre-installed connections.
To date, Simple Life has finished over 40 projects, primarily detached homes and multiresidential buildings. The multiresidental builds can be as tall as six storeys, though Clarke noted the “sweet spot” is three storeys.
“Our building system can be used on all shapes and sizes,” he said, from a four-unit multiresidential building to as big as a 40-unit product.
Its customizable build plans that serve as a baseline include:
- a 1,900-square-foot, four-bedroom home starting from $275,000;
- a three-bedroom farmhouse of over 2,000 square feet starting from $400,000; and
- a 3,400-square-foot fourplex containing three-bedroom units, starting at $350,000.
Simple and sustainable
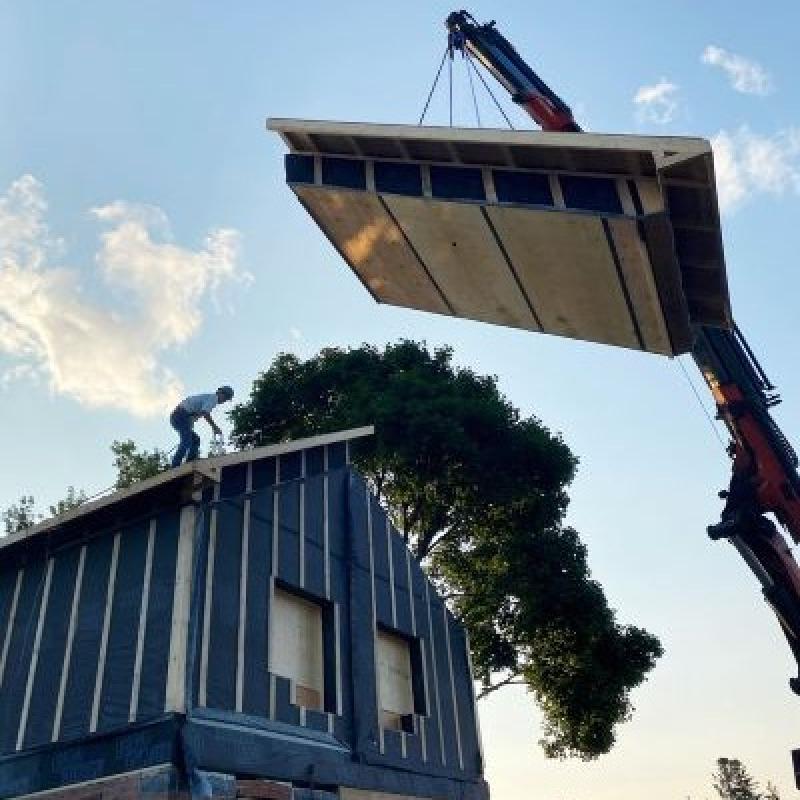
As an example of its speed and efficiency, Clarke recounted a recent 3,000-square-foot home that was assembled in two-and-a-half days, with the components taking approximately six weeks to manufacture.
On price, Clarke said Simple Life aims to be competitive with custom homes by offering a superior value proposition in predictability, sustainability and enhanced comfort.
For sustainability, Clarke said Simple Life’s products are “probably by a factor of five, or maybe even higher, more efficient or sustainable than what the average row home or townhome would be.”
This is largely achieved by its choice of materials that carry low embodied carbon, he said.
For example, Simple Life’s homes use wood fibre board, and densely packed cellulose insulation rather than Styrofoam. Thus, the average Simple Life home traps 20 to 30 tonnes of carbon dioxide which might otherwise go into the environment.
During manufacturing and construction, waste is minimized in a controlled environment which employs modelling software to precisely plan out the production of homes.
Applying Passive House design principles that prioritize air tightness and heavy insulation, plus high-performance windows and doors and heat recovery ventilation systems, Simple Life’s homes are 90 per cent more energy efficient than traditional code-built homes.
Prefabrication should not be fringe, Clarke says
In 2017, the company built its first prefab home and it now turns out about 10 homes annually (based on an average of about 3,000 square feet per residence). It has grown to a team of approximately 10 employees.
Customers include individual home buyers as well as general contractors and developers.
Simple Life’s homes have been sold in Ontario, Quebec and Michigan, with Clarke having an eye for entering Atlantic Canada this year – Nova Scotia and possibly New Brunswick, he explained.
To ramp up its manufacturing capability, Simple Life will be implementing more automation at its Brighton facility in 2026, an evolution that is of great excitement to Clarke. He also plans to further grow the company’s headcount.
Another major plan for next year is to launch a licensing program he hopes to “have available to other people who want to start their own facilities to replicate what we’re doing here.”
To incentivize prefabricated homebuilding, Clarke urges a mix of zoning reform, streamlined permitting for prefab-certified systems, performance-based incentives like the Canada Mortgage And Housing Corporation’s MLI Select program, and more support for off-site manufacturing research and development and workforce training.
“Prefab homes shouldn’t be treated as fringe — they should be recognized as a critical piece of modern housing infrastructure,” he said.