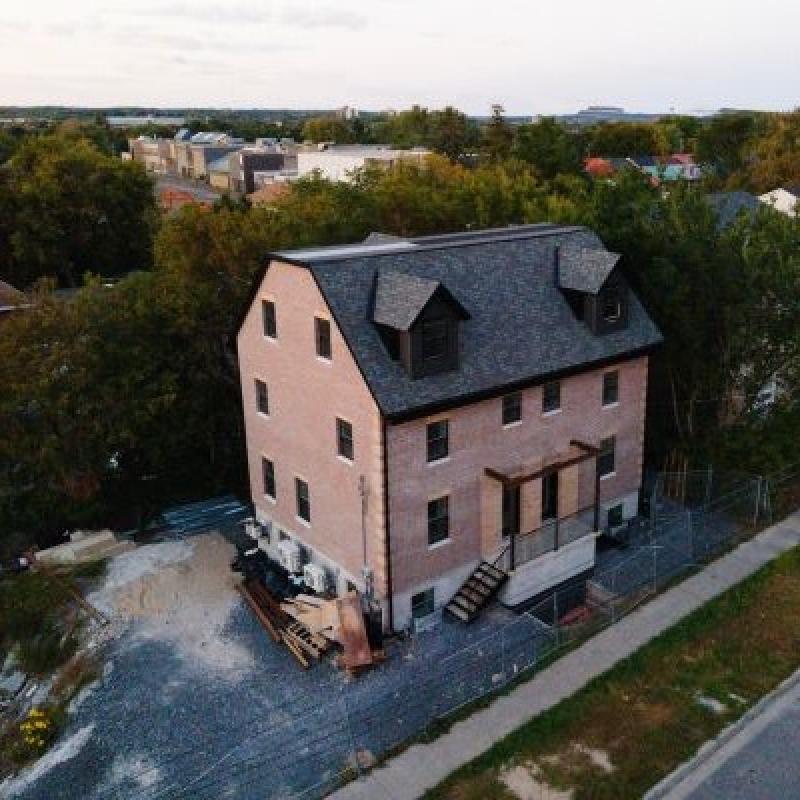
nidus3D, a Kingston, Ont.-based company which constructs buildings via 3D printing, says it has set a new milestone with North America’s first three-storey residential building. The four-unit dwelling also includes a 3D-printed basement.
The almost 6,000-square-foot building (including the basement) in the eastern Ontario city consists of two basement suites and two four-bedroom apartments in the main building, according to Ian Arthur, nidus3D’s president and co-founder.
Houses are 3D printed using technology from Danish company COBOD. nidus3D sets up a rectangular metal frame on the construction site to support a printing robot that extrudes concrete in layers via a nozzle to form the structure of the building.
The latest project beats nidus3D’s previous height record set in 2022 at a property on Wolfe Island, which is adjacent to Kingston in the St. Lawrence River, where it meets Lake Ontario.
“We’re showing the potential of the technology for being able to offer those buildings,” Arthur said in an interview with RENX Homes.
3D printing a three-storey building
Named A&D, the building was constructed in Kingston because it is the company’s primary market and headquarters. Arthur said nidus3D heard about the project and approached the developer for an opportunity to 3D print the building, and found a receptive audience.
A printable area of 39 feet by 38 feet was established on the site, where the 3D printer piped out locally sourced concrete to build the walls. Arthur said the printing took less than one month, with the remaining work like pouring floors requiring over a month.
Unique to the building is its 3D-printed walk-out basement. “Because we have to be able to get the extrusion head down to the poured foundation, we had to over-excavate the hole, drop the printer down below grade and print the basement veneers, and then we grouted the basement,” is how Arthur described the process.
nidus3D’s role in the construction was finished in February, with trades work to complete the building now taking place. Occupancy is expected in the coming months, Arthur said.
When asked if nidus3D learned anything new or faced challenges in constructing A&D, Arthur said the colder weather forced the company to change how it printed, and working at taller heights also required some adjustment to the print speed. But overall, the challenge “was nothing we couldn't overcome,” he said.
The record-breaking claim is verified by COBOD, Arthur said, adding that there are very few completed 3D-printed buildings in North America, making comparison easy.
Faster, greener, more efficient
3D printing has begun to emerge as a way to build housing quicker than traditional methods. For example, Arthur said 3D printing A&D took half as much time compared to stick-frame building methods.
Calling the technology a “transformational paradigm shift” and having the potential to transform the construction sector, the former Ontario government MP said it accelerates and enables construction in locations lacking in skilled construction workers, which is particularly relevant in light of Canada’s housing supply and skilled labour shortages.
“We have what I would call a fundamental process problem in how we build homes,” he said. 3D printing can simplify the complex process, for example, by using far fewer materials in contrast to traditional homebuilding techniques.
That resource efficiency extends to its sustainability. Arthur said there are efficiencies in building performance and the company is actively working to reduce the embodied carbon from the concrete itself.
In a previous interview with Sustainable Biz Canada, Arthur highlighted how his company’s 3D-printed buildings produce minimal construction waste. He also explained that 3D printing cuts transportation emissions, can help construct climate-resilient buildings, and offers the option of recycling building materials.
Looking for more government support
Outside of Kingston, Nidus3D finished a multiresidential project of four buildings on Siksika Nation territory in Alberta. It represents the company’s first multi-print project, and nidus3D hopes to scale its 3D printing to having over 40 buildings on one site.
As an evangelist for the technology, Arthur said its growth will require more government support, including financial support for research and aligning national and regional building codes to allow 3D construction printing.