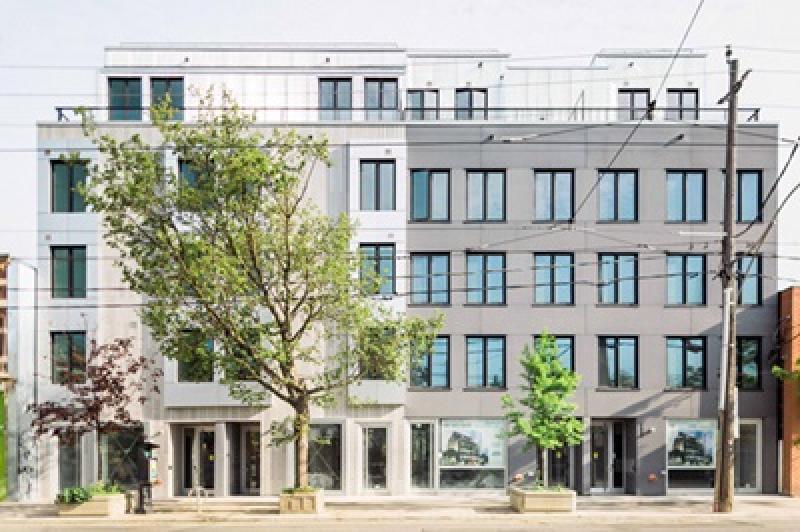
Assembly Corp. is using modular construction materials and techniques to fill the “missing-middle” housing gap by delivering mid-rise, laneway, garden suite and other more affordable housing projects and developments.
“It is about finding a new way to deal with the complicated challenge of mid-rise, which is typically almost an impossible product for building economics,” chief executive officer Geoff Cape said during a panel at the recent Land & Development conference at the Metro Toronto Convention Centre.
The use of building information modelling and other parametric design software enables Assembly’s team members to collaboratively configure and design buildings. Its digitally designed assets include bathroom and kitchen pods, floor cassettes, wall and ceiling panels, facades with cladding and panel assemblies.
These repeatable building components are configured to meet a project's unique needs and enable customizable finishings and facades.
Parametric modelling allows Assembly to see and test the end product, make site-specific changes and test project pro formas at the same time, which reduces the design timeline by 60 per cent.
Reduced construction times and costs
The process employed by Toronto-based Assembly reduces costs by standardizing the building components that are created at partner Fab Structures' factory in Alcove, a Quebec community located north of Ottawa. They're then shipped to building sites where they’re put together.
Assembly’s goal is to open a micro-factory in Toronto as a last-mile logistics hub and assembly facility for just-in-time delivery to building sites to further improve efficiency.
On-site material waste is already reduced by 80 per cent and on-site labour is reduced by 50 per cent from conventional construction using Assembly’s model, according to its website. Cape said Assembly is looking to further accelerate the process by introducing more automation.
“We’ve been working with Danish architects and Swedish logistics and DfMA (Design for Manufacture and Assembly) designers for manufacturing assembly,” Cape said. He noted 85 per cent of residential buildings in Sweden are built in factories and delivered to sites.
Cape said Assembly can often construct an eight-storey building in less than half the time it would take using more common methods. Construction costs are about $400 per square foot.
“When you insert these buildings into the urban fabric, you need to be able to put them together quickly on-site,” Cape explained. “A mid-rise product being inserted on a busy main street has to go up fast because you can’t afford to block off traffic and deal with all the access and egress issues.”
Sustainable and environmentally friendly
Assembly builds with Canadian wood, which reduces embodied greenhouse gas (GHG) emissions by 40 per cent from the levels produced using concrete and steel. Its thermal ratings exceed building code requirements for energy efficiency, which also reduces GHG emissions and utility costs.
“You're surrounded by wood when you're in these places and the feeling is visceral,” said Cape, who previously founded Evergreen and Future Cities Canada. “You feel like you're in a different type of space and the quality of living in these is real.”
Assembly has estimated there’s between $50 billion and $60 billion of mid-rise building construction opportunities just in Toronto.
“The tailwind for mid-rise modular construction is significant,” Cape said, adding that recent federal, provincial and municipal government policies have opened up new possibilities for expansion.
Assembly has built six buildings and has 12 others in production and development.
“Almost all of our clients have been not-for-profit housing corporations that need a turnkey provider,” Cape explained. “We're just beginning to work with the private market for developing purpose-built rental.”
Cape said Assembly’s buildings provide an internal rate of return in the low teens and “to buy and hold these for the long term is actually a good return on your investment.”
Assembly projects
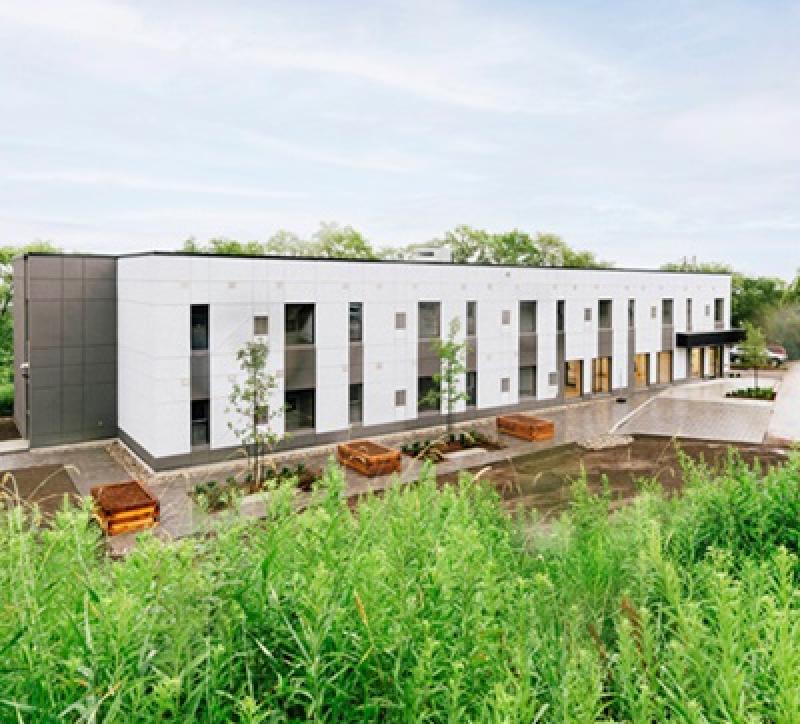
The Passage House — a two-storey, 11,000-square-foot transitional housing project with 18 units in East Gwillimbury just north of the Greater Toronto Area — was completed in seven months.
A two-storey, 7,307-square-foot affordable housing project with 15 units in Hagersville, Ont., was built in eight months.
Among Assembly’s affordable housing projects in progress are:
- an eight-storey, 34,668-square-foot building with 50 units at 60 Bowden St. in Toronto;
- seven semi-detached bungalows with 14 units combining for 8,600 square feet at 1258 Rebecca St. in Oakville;
- a six-storey, 17,986-square-foot building with 20 units at 2217 Kingston Rd. in Toronto;
- a three-storey, 7,362-square-foot building with 27 units at 1120 Ossington Ave. in Toronto;
- a six-storey, 9,996-square-foot building with 15 units at 412 Barton St. in Hamilton;
- an eight-storey, 25,026-square-foot building with 32 units at 215 Wellesley St. E. in Toronto;
- and a six-storey, 18,354-square-foot building with 31 units at 7 Vanauley St. in Toronto.
A six-storey, 13,126-square-foot multifamily building with commercial space at grade took nine months to construct at 1598-1602 Queen St. E. in Toronto. Next door, a companion six-storey, 13,036-square-foot multifamily building with commercial space at grade also took nine months to build at 1602-1604 Queen St. E.
Assembly built a two-storey, 600-square foot laneway suite in Toronto’s Riverside neighbourhood and has four more two-storey laneway and garden suites — ranging from 1,040 to 1,280 square feet — planned in the city.